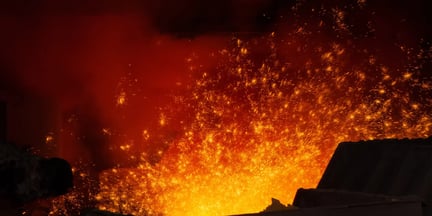
Décarbonation des équipements de procédés à haute température
Dans l'effort collectif de décarbonation de nos industries, certains secteurs sont confrontés à des défis plus importants. Ces secteurs dits « difficiles à décarboner » sont caractérisés par des émissions de carbone liées aux procédés et d'autres polluants atmosphériques dangereux, avec peu d’options simples pour des réductions significatives des émissions.
Ces secteurs concernent principalement la transformation de matières premières dans des environnements à haute température, à l’aide de fours, de calcinateurs ou de fonderies.
La décarbonation des équipements de procédés à haute température constitue un défi majeur dans ces industries. Une bonne compréhension de la fiabilité et de la productivité des équipements de procédé peut contribuer à accélérer la décarbonation de ces installations. Cet article offre un aperçu des différentes voies de réduction des émissions, de leur potentiel et de leurs défis.
Alors que la décarbonation des équipements de procédé à haute température est en pleine évolution, les paragraphes suivants offrent un premier aperçu des différentes des voies de réduction des émissions, de leurs promesses et de leurs défis
Procédés et options de voies de décarbonation
Pour comprendre les voies de la décarbonation, il est essentiel d'examiner les industries clés et leurs procédés, ainsi que les perspectives sur les voies les plus viables et les raisons pour lesquelles elles le sont. Bien que les procédés mentionnés ci-dessous ne soient pas identiques les uns aux autres, il est important d'en apprécier les similarités, car cela crée des opportunités d'apprentissage au sein même des secteurs et entre eux. L'accent est mis sur les émissions provenant des équipements de procédés à haute température, en tenant compte des éléments suivants :
- Les procédés électrifiés devraient utiliser de l'énergie verte.
- Il y aura d'autres émissions distribuées sur le site.
- L'efficacité énergétique profonde devrait toujours être prioritaire.
Les voies de décarbonation évoquées n'incluent pas les procédés nouveaux et innovants spécifiques à certaines industries, comme Elysis pour la production d'aluminium ou Electra pour la production de plaques de fer à basse température.
Cuivre et nickel
Le cuivre et le nickel se retrouvent parfois dans les mêmes gisements de minerai, sont traités de manière similaire et utilisent souvent les mêmes équipements. Ces deux métaux peuvent se présenter sous deux types de gisements différents au Canada, bien qu’ils se trouvent généralement dans un corps de minerai riche en soufre et en fer. Ce qui rend cela intéressant du point de vue des émissions de gaz à effet de serre (GES), c'est que l'oxygène (O₂) peut réagir avec les minéraux sulfurés pour générer de la chaleur lors du processus. Une manière très simplifiée de comprendre le traitement des sulfures de cuivre ou de nickel est la suivante :
Après le processus initial de séparation physique (concassage/broyage, flottation), ces métaux sulfurés peuvent soit être lixiviés pour produire de l'acide sulfurique ou du soufre élémentaire, qu’il faut géré, soit, plus couramment, faire l'objet d'une fusion éclair à plus de 1200°C. Lors de la fusion, c’est à ce moment que l'oxygène est introduit pour éliminer le soufre et le fer, où le concentré réagit pour former du dioxyde de soufre et une couche de scories de silicate de fer qui sont ensuite éliminées. La matte obtenue (50-70% de cuivre ou de nickel) est ensuite traitée soit par lixiviation avec de l'hydrogène comme réducteur pour produire du sulfate d'ammoniaque, soit passée dans un four convertisseur où de l'oxygène est injecté pour oxyder le soufre et le fer restants. Cela produit un métal pur à 96-99 %, qui est ensuite raffiné davantage par hydrométallurgie (lixiviation à l'acide sulfurique ou à l'ammoniaque) ou par pyrométallurgie dans un processus d'affinage électrolytique, donnant ainsi un cuivre ou un nickel pur à 99,99 %. Bien que le processus de raffinage soit alimenté par électricité, la chaleur pour la fusion et la conversion provient de la combinaison d'un combustible et de l'oxygène, contribuant ainsi aux émissions directes de CO₂.
Aluminium
Le processus de production de l'aluminium comporte quatre étapes initiales : la digestion, la clarification, la précipitation et la calcination. L’alumine est générée lors du processus de calcination, puis subit une réduction électrolytique finale dans une installation distincte :
La bauxite est digérée dans un autoclave, chauffée à la vapeur à basse température (240°C) avec l’ajout d'hydroxyde de sodium. Elle est ensuite clarifiée, précipitée et calcinée à des températures allant jusqu'à 1100°C lors d'une étape finale de chauffage appelée «pop-corn». L'alumine est ensuite réduite en métal d’aluminium pur par électrolyse dans des «pots» d'aluminium, où l'oxygène réagit avec les anodes en carbone pour former du dioxyde de carbone. Bien que ce CO₂ soit libéré sous forme pure à partir des anodes, il se combine avec l’air entrant pour générer un gaz de combustion à faible concentration de CO₂. La coulée, en tant qu'étape finale, nécessitera à la fois un préchauffage de l'aluminium pour éliminer l'eau et un four pour couler les lingots d'aluminium, généralement alimenté au gaz naturel.
Fer et acier
Aujourd'hui, le minerai de fer est progressivement chauffé à 1320°C dans un four de durcissement pour produire des boulettes, qui sont ensuite transformées en acier, le plus souvent par le biais d'une aciérie intégrée dotée d'un haut fourneau et d'un convertisseur basique à oxygène. Un haut fourneau est une structure cylindrique de grande taille, revêtue de briques réfractaires capables de résister à des températures élevées, ainsi que d'un élément de refroidissement (bâche). Il convertit le minerai de fer en fonte brute et en scories en fusion, un produit intermédiaire à haute teneur en carbone. Le minerai de fer, le coke et le calcaire sont superposés (chargés) dans le haut fourneau et de l'air chaud est soufflé dans le four pour enflammer le coke à des températures élevées (~2 000 °C). Le coke réduit ensuite les oxydes de fer, puis les scories en fusion et la fonte brute sont extraites par lots. Le calcaire réagit avec les impuretés (par exemple, la silice) pour former des scories qui flottent sur le fer en fusion. La fonte brute produite dans un haut fourneau est ensuite transférée dans un convertisseur basique à oxygène (BOF), où de l'oxygène pur est soufflé dans le métal en fusion, réduisant ainsi le carbone et les impuretés pour produire un produit final en acier.
La croissance de la production d’acier se fera toutefois par le processus de réduction directe du fer (DRI), qui produit une éponge de fer qui, bien qu'utilisant historiquement le charbon ou le coke comme réducteur efficace, utilise de plus en plus le gaz, avec une attention particulière pour l’utilisation de 100% de H₂ comme réducteur. Le DRI à base de gaz se fait généralement dans un four à cuve à une température d'environ 800 à1 100°C, bien qu'une option de lit fluidisé soit en pleine émergence et fonctionne à des températures plus basses. Le produit de fer en éponge par le DRI est soit envoyé directement dans un four à arc électrique adjacent, souvent avec de la ferraille d’acier, soit expédié sous forme de fer briqueté à chaud (HBI) vers un four à arc électrique ou un haut fourneau. Si le minerai de fer dans un DRI est de qualité inférieure (<65 % de fer), le DRI devra d'abord être fondu pour éviter une grande quantité de scories.
Note : Les émissions de CO₂ sont générées à la fois par les réactions chimiques d'un réducteur à base de carbone et par l’apport de chaleur, mais la quantité et la proportion dépendront des types de réducteur et de combustibles utilisés.
Chaux et ciment
Les fours à ciment et à chaux sont de longs fours industriels réfractaires à rotation lente utilisés pour transformer les matières premières en clinker (production de ciment) ou en chaux (production de chaux). Bien que leurs principes de fonctionnement soient similaires, ils diffèrent en termes de matières premières, de réactions chimiques et de produits finaux.
Les fours à chaux produisent de la chaux vive (CaO) en décarbonant le calcaire, qui est chauffé à des températures de 900 à1 000°C, se décomposant en chaux vive et libérant du CO₂. Contrairement aux fours à ciment, les fours à chaux s'arrêtent à la calcination sans former de composés complexes. Le four est généralement soit un cylindre rotatif similaire à celui d’un four à ciment, soit un four statique vertical où le calcaire descend à contre-courant des gaz chauds.
Les fours à ciment, quant à eux, produisent du clinker, le produit intermédiaire de la fabrication du ciment. Un mélange de calcaire, d'argile, de silice et d'oxyde de fer est utilisé comme matière première. Les produits sont séchés et préchauffés dans une tour de préchauffage ou un calcinateur en utilisant la chaleur résiduelle du four. Ce "cru" est ensuite calciné à environ 900°C, où le calcaire se décompose en chaux, libérant du CO₂. La chaux réagit ensuite avec d'autres composants à 1450°C pour former des minéraux de clinker. Divers types de combustibles sont actuellement utilisés, tels que le charbon et le gaz naturel, de plus en plus complétés par des combustibles alternatifs tels que les pneus en fin de vie ou les déchets biogènes tels que la biomasse ligneuse ou même les déchets d'abattoir.
Réflexions
Des voies techniquement prometteuses, mais économiquement difficiles existent pour tous les procédés, certaines étant plus applicables que d'autres en fonction du procédé et du contexte local. Des dépenses d'investissement et d'exploitation importantes seront nécessaires. La capture du CO₂et/ou l'oxycombustion, ainsi que l'hydrogène, sont des voies cohérentes disponibles pour toutes les options. La collaboration à grande échelle est essentielle pour décarboner efficacement les procédés à haute température. Toute solution doit faire l'objet d'une quantification des émissions sur l'ensemble de son cycle de vie afin de comprendre les réductions nettes globales.
Note : Cet article reconnaît qu'il peut exister d'autres voies et d'autres perspectives qui ne sont pas couvertes. Il reconnaît également les limitations et le contexte des explications en raison de la brièveté de l'article. Toute erreur est attribuée uniquement à l'auteur, qui remercie les personnes ayant contribué à l'élaboration de l'article.
Auteur
Matthew McCulloch
Responsable de la décarbonation chez Norda Stelo