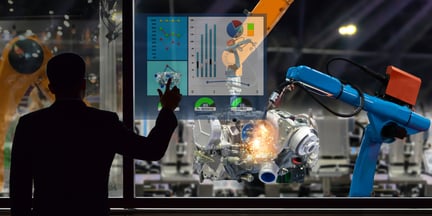
Industrie 4.0 et transformation numérique: quels sont les enjeux critiques d’aujourd’hui?
La transformation numérique de l’industrie lourde et des entreprises manufacturières constitue une véritable occasion de développement pour le secteur manufacturier et la croissance économique du Québec. Et comme avec toute transformation, celle-ci vient avec son lot d’enjeux et de défis.
Dans un monde en changement où plusieurs opérations se font à distance, et même en télétravail, il est primordial de mettre les données au cœur de votre stratégie de transformation numérique.
Depuis moins d’une décennie, l’internet des objets, l’industrie 4.0 et la transformation numérique bouleversent les entreprises et engendrent des changements radicaux, non seulement aux systèmes et aux processus, mais également aux modes de gestion, aux modèles d’affaires et à la main-d’œuvre. L’évolution rapide des technologies, la transformation des métiers et les nouvelles exigences des clients poussent aujourd’hui l’industrie à remodeler son usine pour devenir plus innovante, plus compétitive et créatrice d’emplois.
Cette transformation se définit essentiellement par l’intégration de nouvelles technologies à la chaîne de valeur de l’entreprise. L’exploitation et la gestion massives des données (Big Data), l’interconnexion des machines (Industrial Internet of Things – IIOT), l’automatisation et la robotisation permettront une production plus flexible et personnalisée pour l’avenir.
Dans les faits, les besoins sont uniques à chaque entreprise et il est préférable d’être réaliste sur ses ambitions, car la mise en place d’une stratégie numérique intégrée à la stratégie d’entreprise, incluant l’acquisition de nouvelles technologies, représente plusieurs enjeux pour les gestionnaires.
Au départ, en ciblant de petits objectifs de transformation, cela permettra d’obtenir de rapides gains de productivité et souvent avec un minimum d’investissement. Voici certains des enjeux critiques où Norda Stelo peut vous accompagner :
1. L’amélioration de la productivité en valorisant les données
L’adoption des technologies numériques procure une longue liste d’avantages, parmi lesquels une augmentation substantielle de la productivité, du chiffre d’affaires, de la qualité des produits et de la satisfaction globale de la clientèle.
Selon un sondage récent de la Banque de Développement du Canada mené auprès de quelque 1 000 entrepreneurs, 60% des adopteurs affirment que les technologies numériques ont contribué à accroître leur productivité de manière substantielle. De plus, 50% des adopteurs affirment que cela les a aidés à réduire leurs coûts d’exploitation et 42% disent avoir amélioré la qualité de leurs produits.
En premier lieu, il faut identifier les endroits où l’on doit acquérir plus de données pour conduire l’analyse et ensuite, on devient en mesure de prioriser les ajustements nécessaires. De cette manière, on parvient souvent à optimiser rapidement la productivité, et ce, avec seulement de petits investissements.
Les données en temps réel procurerons l’agilité nécessaire pour faire les choix éclairés afin d’anticiper et prévenir des arrêts de production non souhaités, d’optimiser l’efficacité de production et d’améliorer la planification d’entretien des équipements.
La collecte de données en temps réel pour une ligne de production nous donnera la capacité d’adaptation aux changements qui peuvent être causés soit par un bris, une réaction anormale du procédé ou encore une opération fautive. Cette capacité d’adaptation aux changements constitue le fer de lance du virage 4.0.
2. La maintenance et la gestion des actifs
Considérée comme le Graal de la transformation numérique, la maintenance prédictive devient la quête ultime pour détecter les pannes dans le temps et éviter de coûteux arrêts de production non planifiés.
Avec l’installation et la programmation de capteurs et d’instrumentation de mesure, on parvient à sonder facilement les équipements selon leurs conditions réelles d’utilisation. L’analyse des données provenant des systèmes de surveillance permet ainsi de déterminer les facteurs de probabilité d’un défaut et d’intervenir rapidement.
Une autre manière de diminuer les coûts et les impacts de la maintenance des équipements est d’automatiser et de robotiser les tâches d’entretien afin d’obtenir des arrêts de production plus courts et d’éviter les enjeux liés à la sécurité des travailleurs, tels que le travail en espace clos, le travail en hauteur ou dans les environnements à risque.
D’ailleurs, c’est dans cette lignée du virage 4.0 que le Centre d’Excellence « Gestion de l’intégrité et de la fiabilité des actifs » de Norda Stelo a élaboré une nouvelle plateforme collaborative pour la gestion et l’entretien des actifs, destinée à tout type de parcs de réservoirs. Ce nouvel outil combine la puissance des technologies intelligentes et repose sur l’expertise de pointe que Norda Stelo possède depuis plusieurs années en gestion de l’intégrité et de la fiabilité des actifs. Pour plus de détails sur notre plateforme collaborative de gestion des actifs, consultez : https://geniecollectif.norda.com/bilan-de-sante-dun-parc-de-reservoirs.
De plus, dans une optique de partenariat avec nos clients, notre équipe d’experts en maintenance travaille à développer de nouveaux outils qui permettront de guider les opérations de maintenance dans les usines. Actuellement, nous développons un outil utilisant la réalité augmentée afin de faciliter l’entretien des machines et des équipements spécialisés.
3. La sécurité des machines
Plus que jamais aujourd’hui, la gestion de la santé et de la sécurité en usine est une préoccupation de premier ordre et doit faire partie intégrante du processus 4.0. Avec le virage 4.0, la démarche SST pour sécuriser les machines se fera de manière intégrée en tenant compte dorénavant d’une multitude de données qui permettront, par exemple, d’avoir accès à toutes les informations relatives à l’état d’opération en temps réel, facilitant ainsi les interventions préventives sur les machines à risque.
Puisque les données des machines peuvent être toutes compilées sur une plateforme informatique, il devient plus facile de faire l’analyse des impacts, d’apporter des correctifs et de produire un bilan détaillé pour chaque machine. Par exemple, pour des machines autonomes, l’information recueillie pourra servir à contourner et éviter des endroits ou des positions mettant plus à risques la santé et la sécurité des travailleurs.
Forte d’une expertise dans les usines en cours d’exploitation, Norda Stelo accompagne le déploiement des stratégies 4.0 dans le but d’assurer une bonne transition vers ces nouvelles technologies. Notre expertise dans les domaines de l’instrumentation & contrôle, de la robotique, de l’informatique industrielle et des télécommunications est régulièrement mise à contribution afin de répondre aux besoins et aux défis technologiques présents dans les entreprises manufacturières et l’industrie lourde. Prendre le virage 4.0 avec Norda Stelo, c’est compter sur une équipe chevronnée, qui est animée par les nouvelles technologies et appuyée par une solide expérience!
Retour au blogue